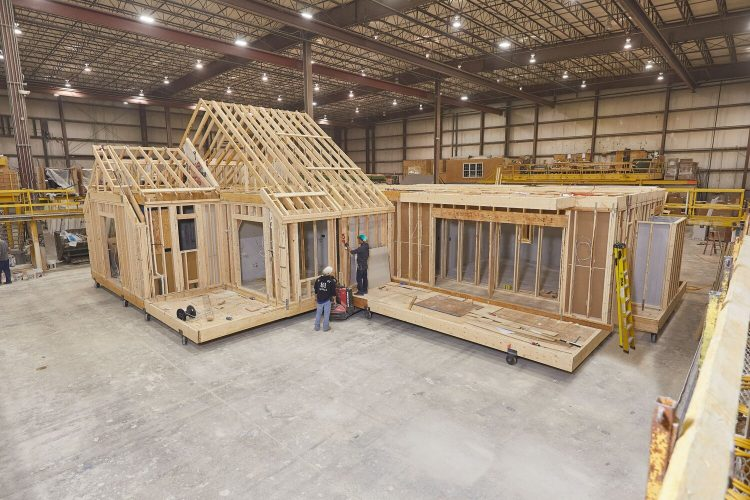
Modular construction is rapidly transforming the building industry, offering a compelling alternative to traditional stick-built methods. With its promise of increased efficiency, reduced costs, and faster project completion, it’s no wonder real estate developers, general contractors, and private equity firms are taking notice. However, successfully navigating the world of modular construction requires careful planning and a clear understanding of the unique processes involved. This blog post will guide you through the key aspects of preparing for a modular construction project, outlining what to expect at each stage, from off-site fabrication to on-site integration.
Off-Site Fabrication: The Heart of Modular Efficiency
The core of modular construction lies in its off-site fabrication process. This involves constructing building modules in a controlled factory environment, often simultaneously with site preparation. Understanding this phase is crucial for setting realistic expectations and maximizing the benefits of modular construction.
One of the primary advantages of off-site fabrication is the enhanced level of control it offers. Unlike traditional construction sites, modular factories provide a sheltered environment, shielding construction from weather delays and minimizing material waste. This controlled setting also allows for tighter quality control, as processes can be standardized and closely monitored. Expect rigorous inspections at various stages of fabrication to ensure modules meet precise specifications and adhere to building codes.
Furthermore, the factory environment fosters greater efficiency. Assembly-line techniques and specialized equipment streamline the construction process, leading to faster production times and reduced labor costs. Expect to see a significant reduction in the overall project timeline compared to traditional methods. The parallel nature of off-site fabrication and site preparation further accelerates the schedule, allowing for simultaneous progress on both fronts.
Another key consideration during the off-site fabrication phase is the level of customization available. While modular construction is often associated with repetitive designs, modern techniques allow for a high degree of architectural flexibility. Expect to work closely with the modular manufacturer to define your design requirements, material choices, and interior finishes. Clear communication and detailed specifications are essential to ensure the final product aligns with your vision.
Finally, it’s important to understand the payment structure associated with off-site fabrication. Typically, payments are tied to specific milestones achieved during the manufacturing process. This may include payments for design completion, material procurement, module fabrication, and quality control inspections. A well-defined payment schedule, outlined in the contract, will help manage cash flow and ensure transparency throughout the project.
Logistics and Delivery: Bridging the Gap Between Factory and Site
The logistics and delivery phase is a critical link between the off-site fabrication and on-site integration stages. Careful planning and coordination are essential to ensure the smooth and timely transportation of modules from the factory to the construction site.
One of the first steps in this phase is to assess the transportation routes and identify any potential obstacles. This may involve evaluating road conditions, bridge clearances, and local regulations. Expect to work closely with the modular manufacturer and a specialized transportation company to develop a detailed logistics plan that addresses these challenges.
The size and weight of the modules will also influence the transportation method. Depending on the project’s location and the dimensions of the modules, transportation may involve trucks, trains, or even barges. Expect to see specialized trailers and lifting equipment used to safely load, transport, and unload the modules.
Coordination with local authorities is also crucial to obtain the necessary permits and approvals for transporting oversized loads. This may involve coordinating with police escorts and scheduling deliveries during off-peak hours to minimize traffic disruptions. Expect the modular manufacturer or transportation company to handle these administrative tasks, but it’s important to stay informed about the progress and any potential delays.
Upon arrival at the construction site, the modules must be carefully unloaded and staged for installation. This requires a designated staging area with sufficient space and a level surface. Expect to see cranes and other heavy lifting equipment used to precisely position the modules for integration.
Finally, it’s important to consider the environmental impact of transportation. Opting for manufacturers located closer to the construction site can help reduce transportation distances and minimize carbon emissions. Expect to see a growing emphasis on sustainable transportation practices within the modular construction industry.
Site Preparation: Laying the Foundation for Success
While modules are being fabricated off-site, the construction site must be meticulously prepared to receive them. This phase is crucial for ensuring a seamless and efficient integration process.
One of the first steps in site preparation is to conduct a thorough site survey and geotechnical investigation. This will help identify any potential soil issues, underground utilities, or environmental hazards that may need to be addressed. Expect to see engineers and surveyors on-site, collecting data and developing a detailed site plan.
Based on the site survey, the foundation must be prepared to meet the specific requirements of the modular building. This may involve excavating the site, pouring concrete footings, and installing utility connections. Expect the foundation to be precisely leveled and aligned to ensure the modules fit together seamlessly.
In addition to the foundation, the site must also be prepared to accommodate the delivery and installation of the modules. This may involve clearing access roads, creating staging areas, and installing temporary utilities. Expect to see heavy equipment on-site, preparing the ground and creating a safe and efficient work environment.
Coordination with local utility companies is also crucial to ensure timely connection of water, sewer, and electrical services. This may involve submitting permit applications, scheduling inspections, and coordinating with utility crews. Expect the general contractor to manage these tasks, but it’s important to stay informed about the progress and any potential delays.
Finally, it’s important to consider the environmental impact of site preparation. Implementing erosion control measures, minimizing dust emissions, and recycling construction waste can help reduce the environmental footprint of the project. Expect to see a growing emphasis on sustainable site preparation practices within the modular construction industry.
Integration and Finishing: Bringing the Modules to Life
The integration and finishing phase is where the prefabricated modules are assembled on-site to create the final building. This phase requires careful planning, precise execution, and close coordination between the modular manufacturer and the general contractor.
Once the modules are delivered to the site, they are carefully lifted into place using cranes and other heavy lifting equipment. The modules are then connected to each other, creating a structurally sound and weather-tight building. Expect to see skilled tradespeople on-site, carefully aligning and securing the modules.
After the modules are connected, the seams between them are sealed and finished to create a seamless appearance. This may involve applying sealant, installing trim, and painting or cladding the exterior walls. Expect the finished building to look indistinguishable from a traditionally constructed building.
Interior finishing work, such as installing flooring, fixtures, and appliances, is typically completed after the modules are integrated. This may involve working with subcontractors to install electrical wiring, plumbing, and HVAC systems. Expect the interior finishes to be of the same quality and craftsmanship as those found in traditionally constructed buildings.
Quality control inspections are conducted throughout the integration and finishing phase to ensure the building meets all applicable building codes and standards. This may involve inspections by the modular manufacturer, the general contractor, and local building officials. Expect any deficiencies to be promptly addressed and corrected.
Finally, landscaping and site improvements are completed to enhance the appearance and functionality of the building. This may involve planting trees and shrubs, installing walkways and patios, and creating parking areas. Expect the finished building to be a valuable asset to the community.
3 Key Takeaways for Modular Construction Success
- Early and Thorough Planning is Paramount: Success in modular construction hinges on meticulous planning from the outset. This includes detailed design specifications, comprehensive site assessments, and a well-defined logistics plan. Engaging with experienced modular manufacturers and consultants early in the process can significantly mitigate potential challenges and optimize project outcomes.
- Communication and Collaboration are Essential: Modular construction requires seamless communication and collaboration between all stakeholders, including the developer, architect, modular manufacturer, general contractor, and local authorities. Establishing clear lines of communication and fostering a collaborative environment will ensure that everyone is aligned and working towards the same goals.
- Embrace Innovation and Adaptability: The modular construction industry is constantly evolving, with new technologies and techniques emerging regularly. Staying informed about these advancements and being willing to adapt your approach can lead to significant improvements in efficiency, cost savings, and project quality.
By understanding the key aspects of preparing for a modular construction project, real estate developers, general contractors, and private equity firms can unlock the full potential of this innovative building method. With careful planning, effective communication, and a willingness to embrace innovation, modular construction can deliver faster project completion, reduced costs, and higher quality buildings.